产品详情
自保温砌块设备产品简介:
自保温砌块设备 替代传统的建筑保温体系:外墙内保温和外墙外保温,外墙自保温实现了保温和墙体的同步施工减少施工工序、缩短建筑工期,缩短施工周期两个月左右,大幅节省保温施工成本;相对于传统外保温,直接成本减少15-20左右;避免外墙保温层脱落隐患,提高建筑质量;保温芯体被混凝土包覆,大幅减少火灾隐患;终实现保温与墙体同寿命以及墙体与建筑主体同寿命;
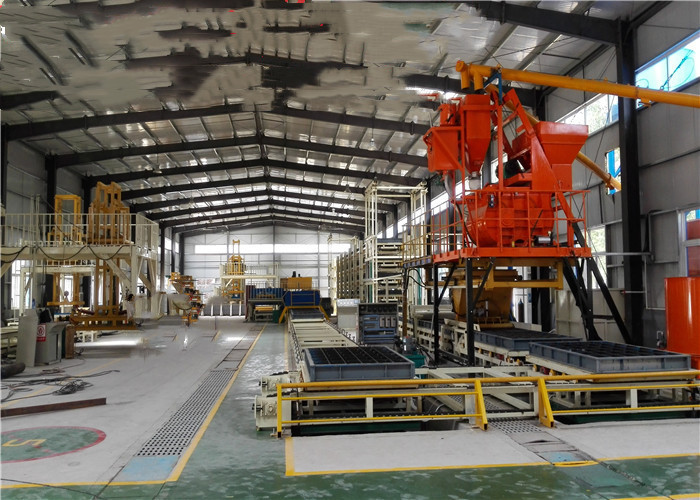
生产和养护:
复合自保温砌块配套生产线具有自动化程度高、生产效率好、组合性强等特点,采用自动配料系统,生产过程全程监控控制,原材料计量精准,产品质量稳定,采用注塑微震成型工艺,无需蒸压、煅烧,降低了生产制备过程的能源消耗和环境污染。自动化生产线包括生产和养护两大部分.
自保温砌块设备特点:
(1)多种传动方式相结合:生产设备采用齿轮传动、气缸传动、链条传动、液压传动、涡轮蜗杆等目前较为先进的多种传动方式方式相结合,保证了砌块生产过程的传输稳定。
自保温砌块生产线
(2)生产线全过程“PLC”控制:生产线完全实现机械化,全程采用监控控制,控制柜分为强电柜和弱电柜,安全性得到有效提高,控制系统采用触摸屏与传统按钮结合的方式,控制更为直观。
复合自保温砌块生产线
(3)自动配料:原材料上料系统完全采用自动计量,实现自动配料,降低了配料中人为因素,提高了产品质量稳定性。
(4)被动式太阳能养护:复合自保温砌块采用太阳能养护,与生产线连接为一体,实现了完全动态搬运,降低了产品破损率。
生产线运行系统:
1. 储料和自动计量:
实现精确计量,减少人工避免物料浪费,全封闭运行,减少环境污染;
2. PLC电脑控制混凝土下料系统:
确保均匀布料,下料准确,实现产品密实,避免大气泡出现导致产品质量不稳定;
3. 全自动生产线运行系统:
摩擦动力轮驱动:
①实现各个环节和工序的独立操控,
②摩擦动力轮实现正反转,便于维修和故障排除;
③与传统汽缸硬顶的形式相比,摩擦动力轮实现软连接,避免破坏性生产事故;精准定位:系统通过限位和电控以及机械定位系统,自动将模具传送至脱模系统;整箱脱模:
4、系统可以自动实现整箱36块脱模,快速高效,一次性整箱脱模数量为行业内大。
5、高位升降系统:
高位升降系系统自动将切块叠成多层,转运到到切块养护车间,单位时间内实现更多切块运转,大幅提升运转效率;
6、自动清洗与覆膜系统
脱模后的磨具自动进入清洗流程,采用行业首创的用双排多头高压喷淋冲洗,全方位无死角,5秒清洗完毕;同时磨具底托自动覆膜,实现磨具底托免清洗化,减少人工投入、减少生产工序;
7、双排或多排整体保温芯体
行业首创一体化整体保温芯体,实现了芯体的精准定位,同时实现保温外壳与芯体的无缝连接,减少人工,提高效率。
8、自动多层预养系统
模具浇筑后自动进入预养仓,多层立体化的预养仓节省了大量的空间,实现一次性大批量砌块预养;
9、太阳能养护线;
生产线厂房设计利用太阳光的力量进行自然养护,比传统蒸养形式大幅节省能源消耗,更有利于项目立项阶段的环评审批,复合发改委对于新型绿色建材的节能标准;
10、自动化程控多排转运车
转运速度快、操控性好,单次转运可以转运砌块3个立方以上,单次转运量为行业内大;
11、自动化成品码垛系统
系统实现自动化5层码垛,提高了码垛效率,节省人工,便于成品快速运离厂房,提高生产效率。
12、底托自动电磁吸附转移系统
系统采用先进的电磁吸附技术,将底托自动吸附转运至生产线上,实现自动流水化循环生产;
设备优势:
设备成熟度与工艺匹配度好;自动化程度高;确保工厂化生产工艺的批量生产,确保产品高性能、高品质;
产品性能高,适用气候恶劣,四季温差大的地区,适用面更广,市场更广泛;
产品指标行业内高,复合全国各省市地方要求;
自动化程度高,自动化程度达到90%以上;